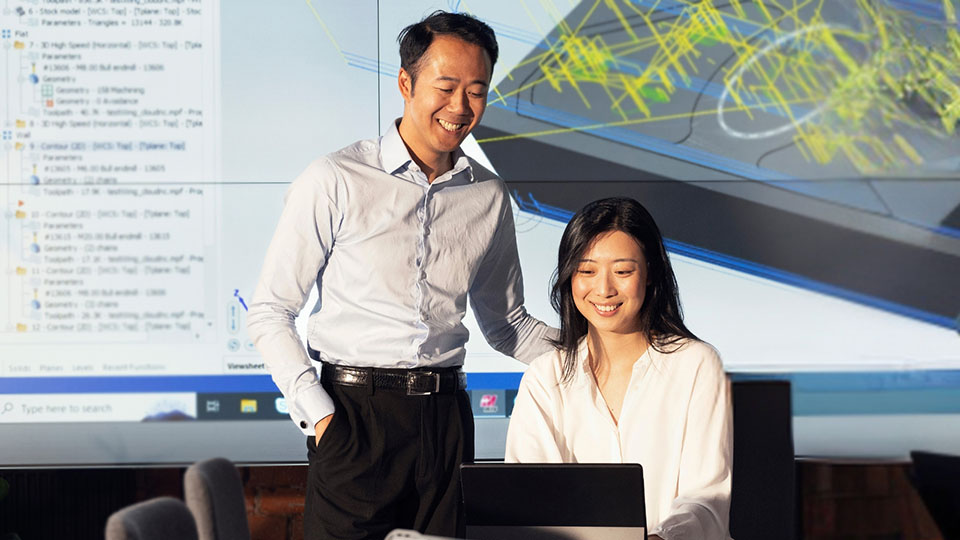
05/27/2025
Sandvik's whitepaper, "Trends in Manufacturing Software Usage," explores how manufacturers are leveraging automation, integration, and AI to address challenges like skilled labor shortages and increasing product complexity.
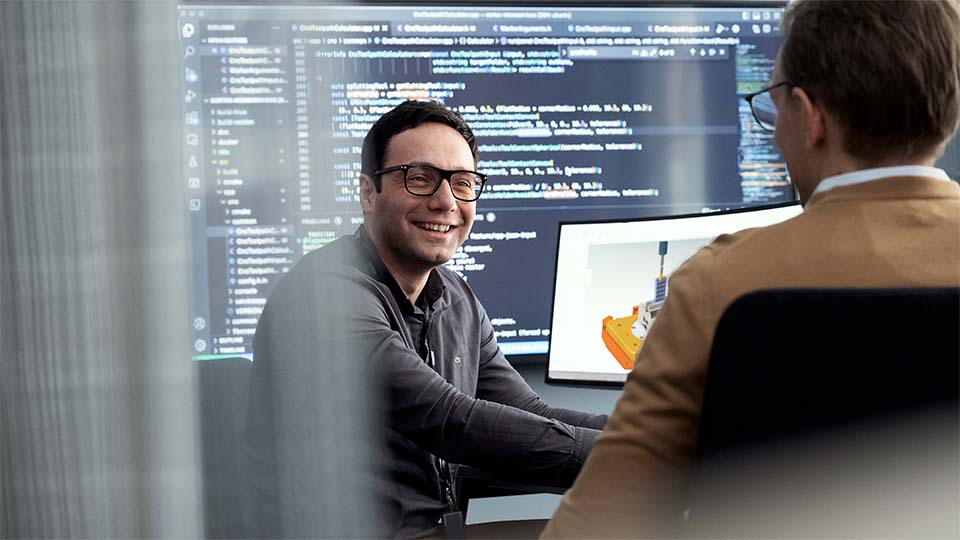
04/08/2025
Sandvik's new white paper, developed with EY-Parthenon, outlines six automation stages in component manufacturing, revealing that 80% of surveyed manufacturers aim to enhance automation by 2030 to boost efficiency and competitiveness.
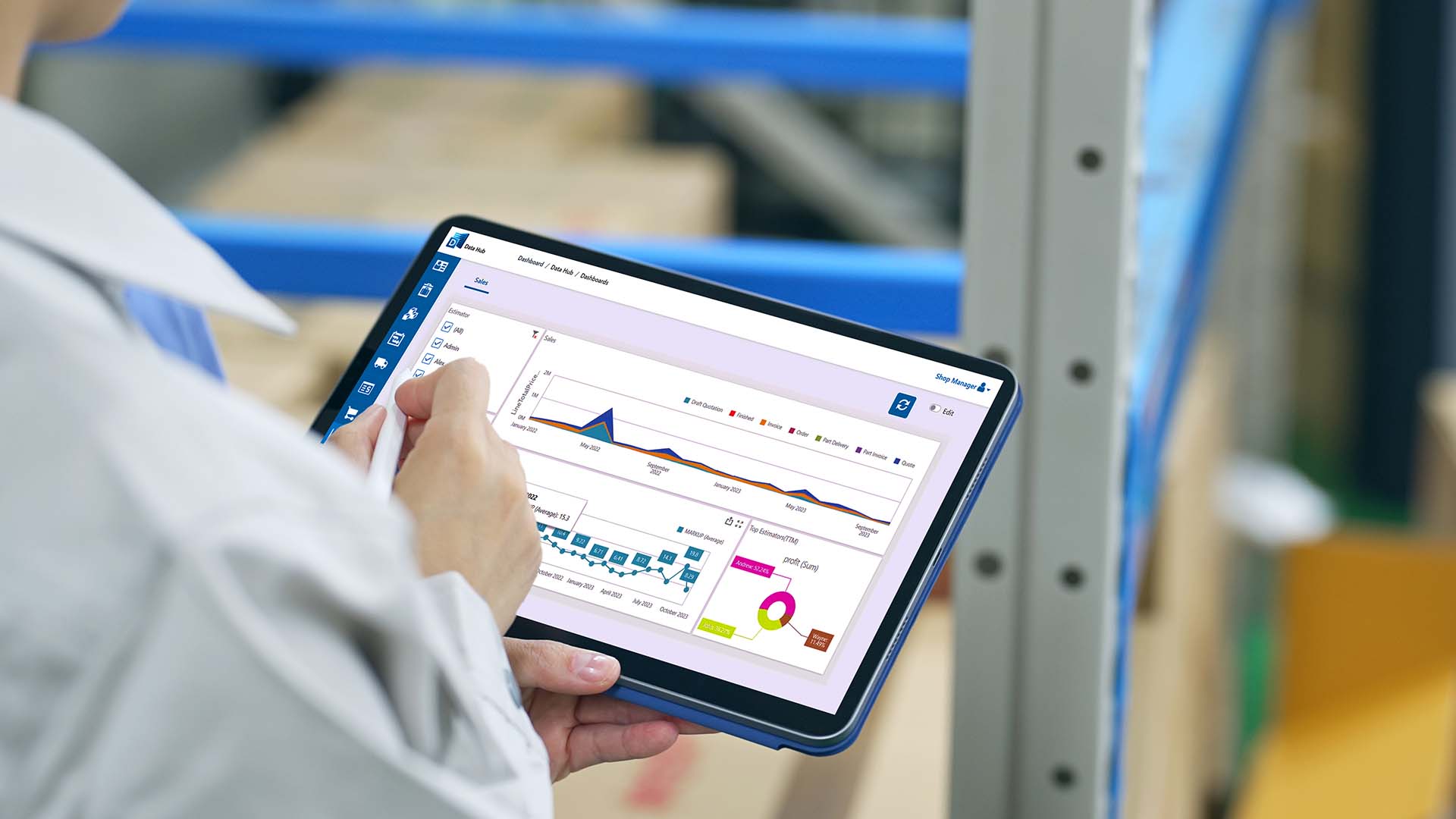
04/15/2024
Transforming data into useful information is simplified with a comprehensive suite of software
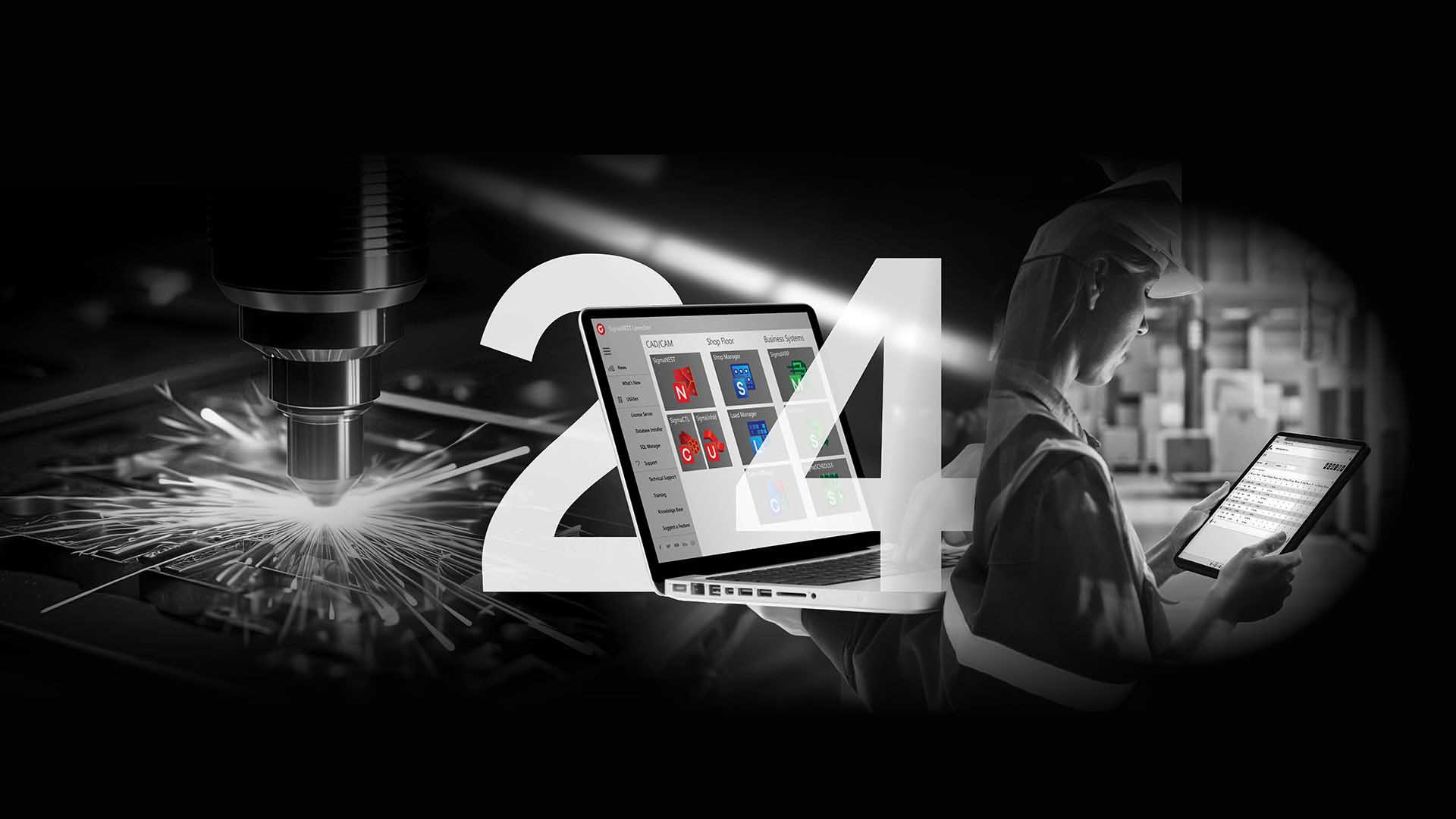
04/04/2024
SigmaNEST, a leading innovator in CAD/CAM, shop floor, and business software for the fabrication industry, is pleased to announce version 24 of the software suite.
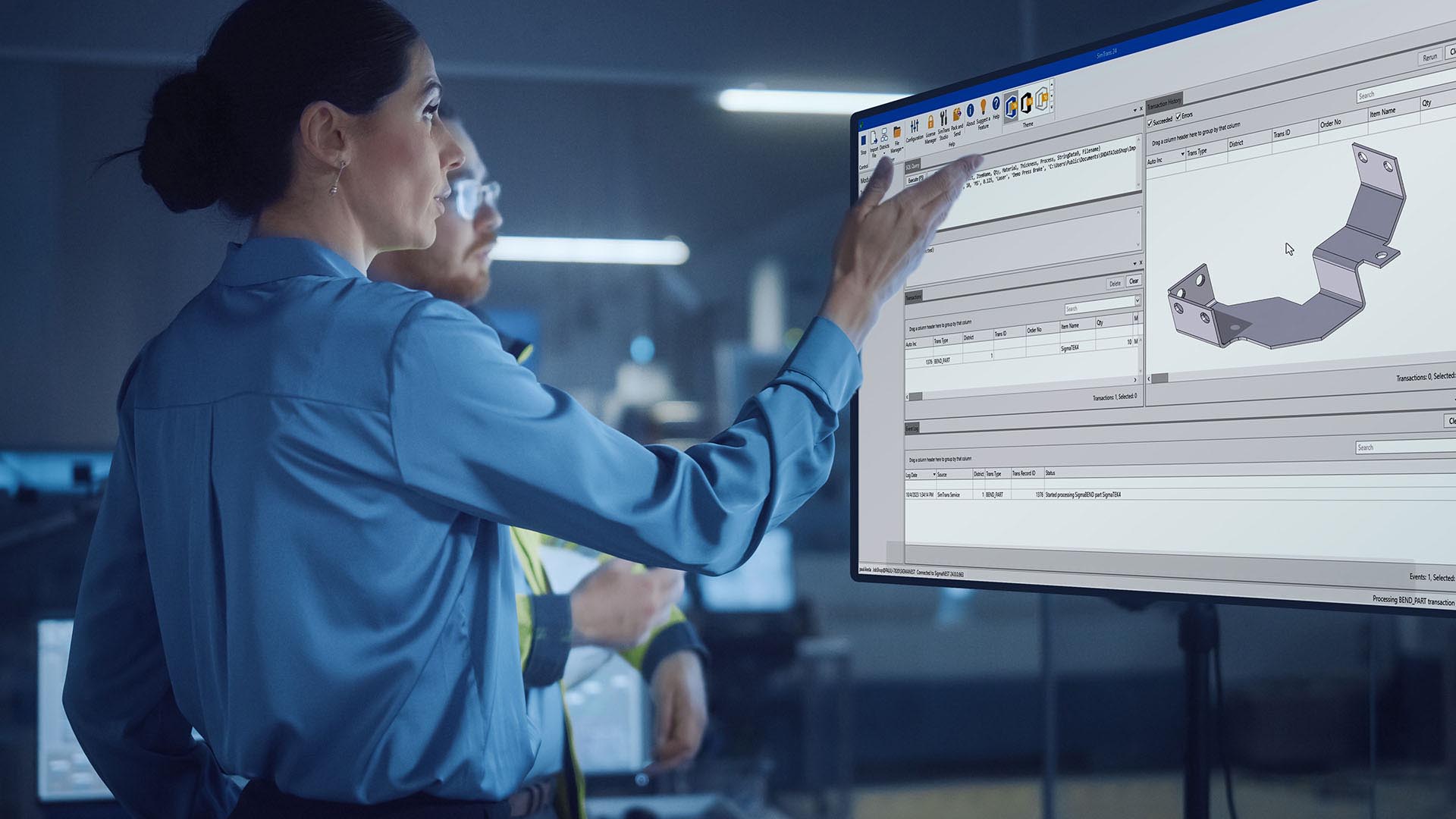
01/31/2024
The 2024 version of SimTrans features a feedback function that reports information back upstream to the parent ERP system.
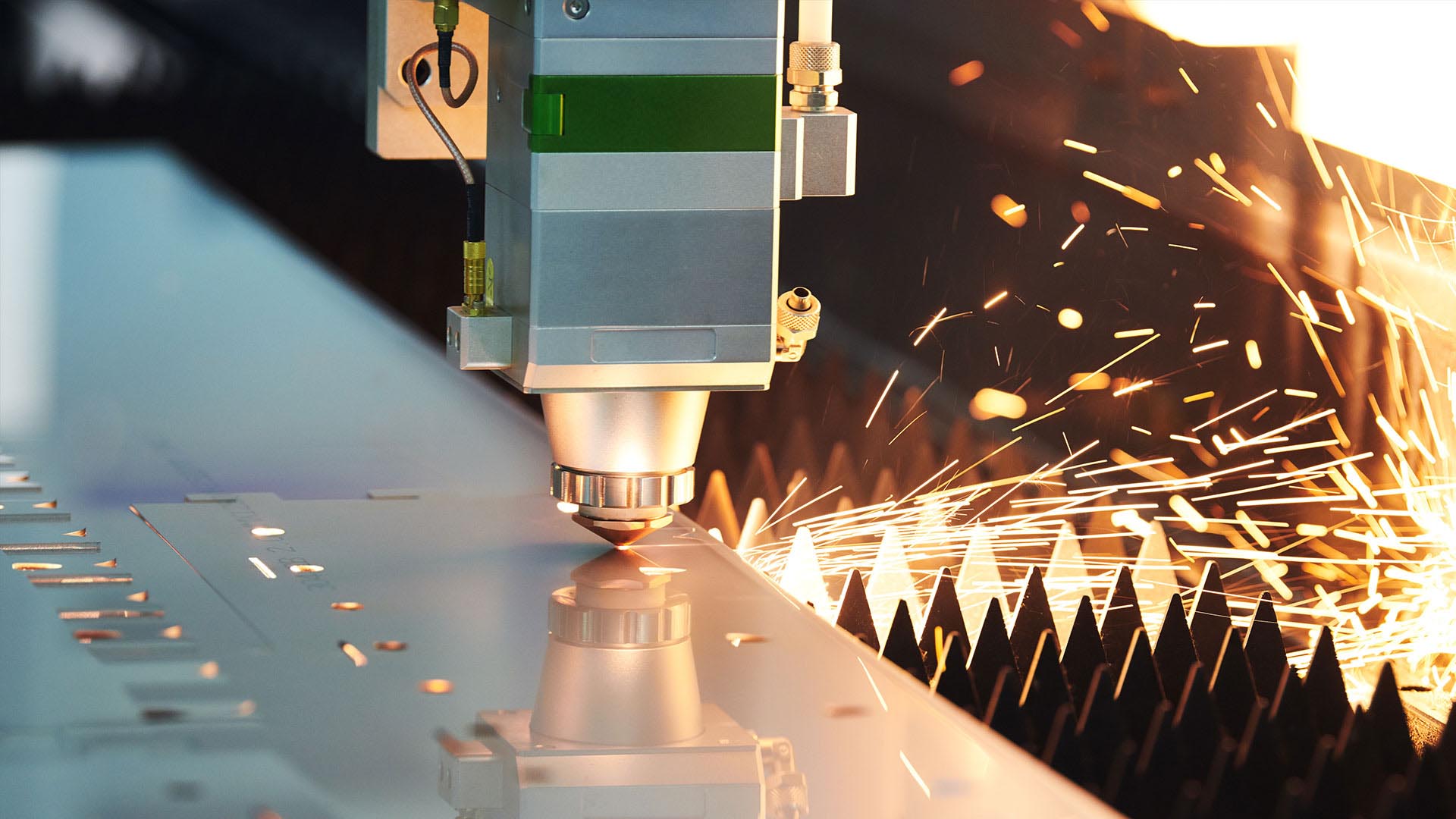
10/12/2022
Nesting has been hailed as one of the most important technologies of the last 30 years for fabricators worldwide. And of course, it's true.
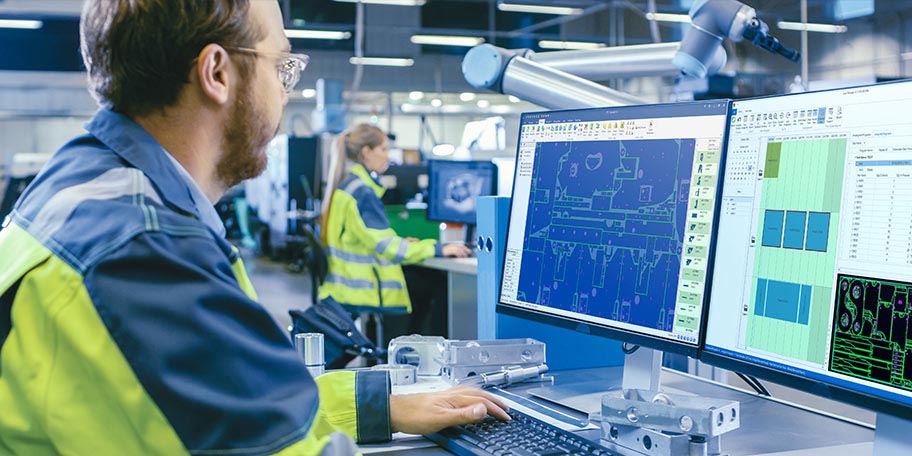
06/29/2022
Fabricators can optimize material usage, machines, manpower and data in the face of supply chain disruptions and labor shortages.

03/21/2022
In the world of nesting, tube can be quite different to work with than plate. With plate, there is a level of nesting freedom that fabricators don’t get with tube.
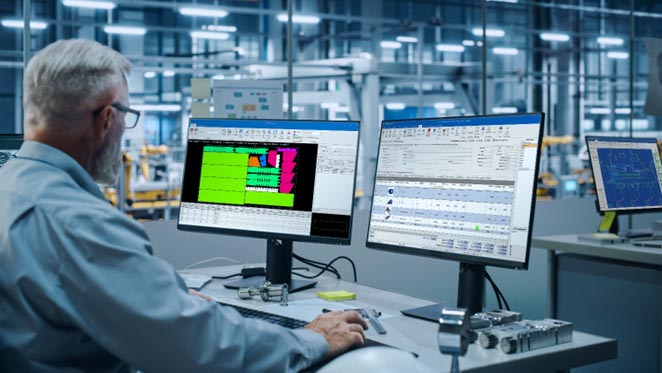
12/20/2021
SigmaSUITE V23 Redefines Nesting Strategies and Process Optimization for Connected Shop Fabrication.
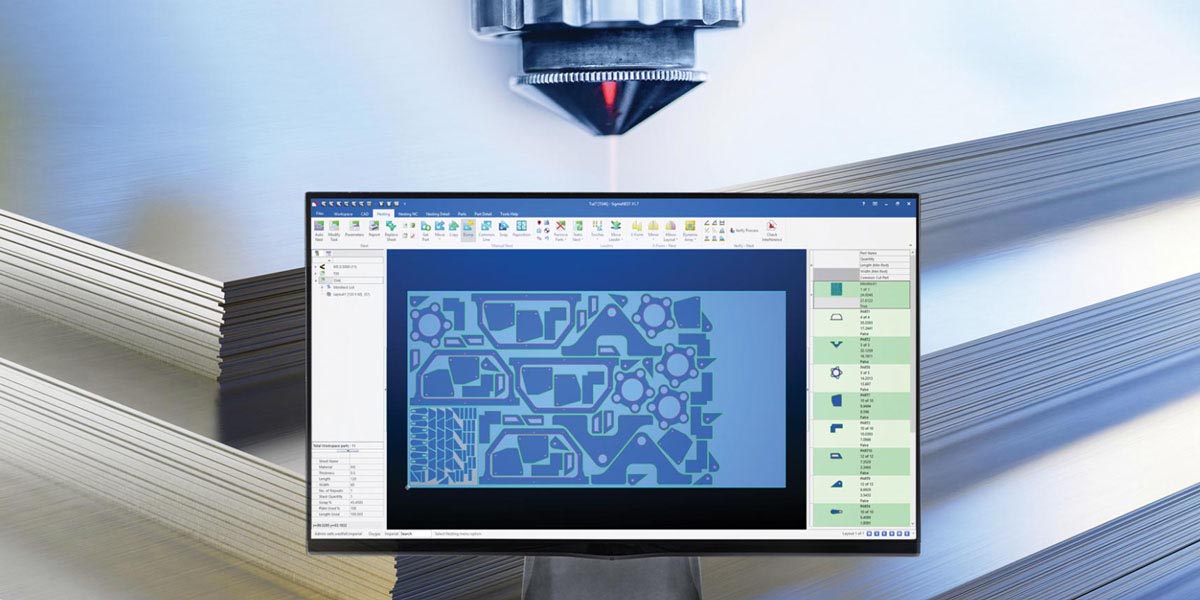
12/20/2021
Service centers make their software platform smarter with CAD/CAM integration.
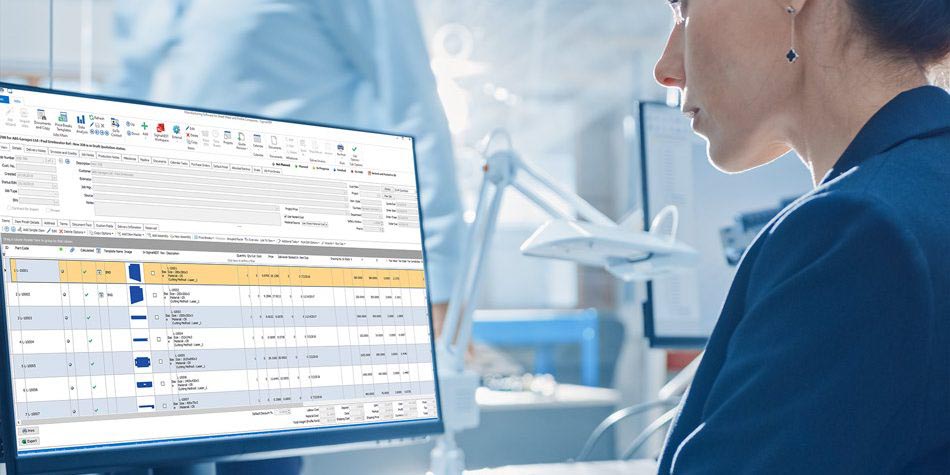
08/20/2021
Win contracts and standardize quoting practices with the latest software options.
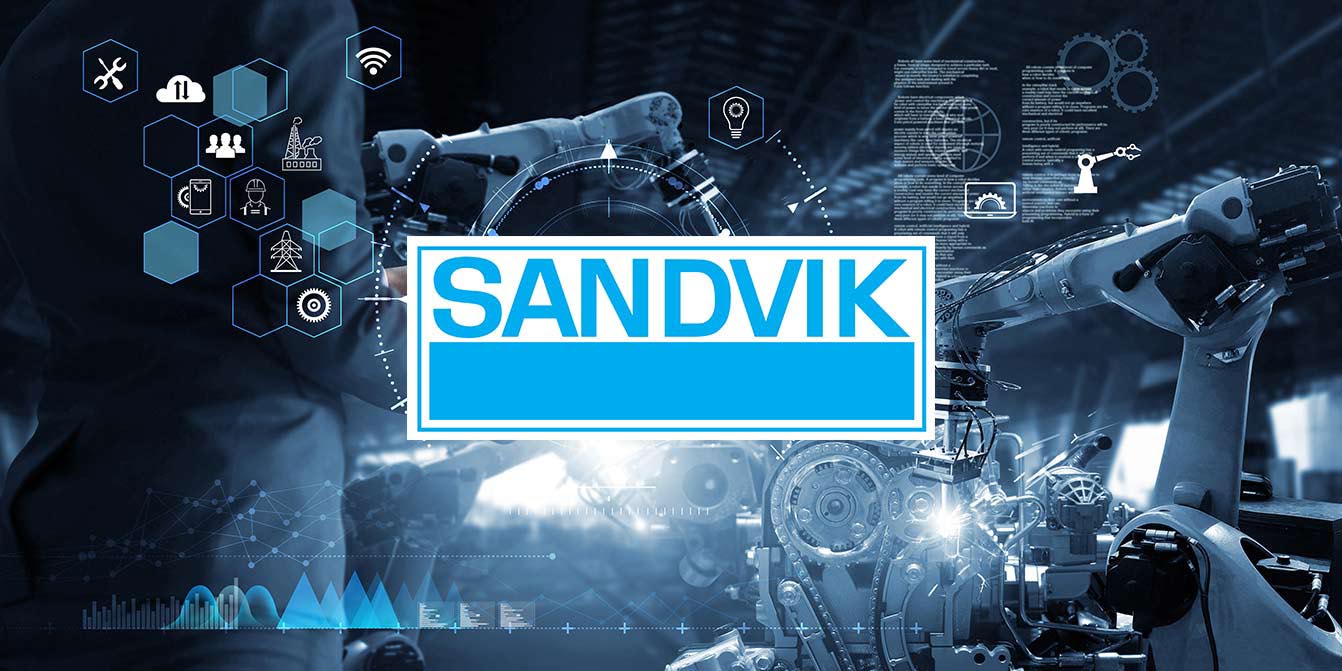
07/01/2021
Sandvik has signed an agreement with Battery Ventures to acquire US-based CAMBRIO, a leading company with an end-to-end portfolio in CAD/CAM software for manufacturing industries like automotive, transportation, energy, medical and aerospace.