Transaction solution links shop activity with front office, automates processes and is compatible with customer systems
Download Article PDFThe 2024 version of SimTrans from SigmaNEST received a significant transformation supporting two key themes: empowerment and reverse reporting. Through real-time processing, SimTrans provides feedback to streamline workflow between different systems and transactions.
SimTrans was designed to connect the myriad ERP systems in the market with the SigmaNEST software from CAD/CAM nesting to shop floor automation and other business systems. “It supports fabricators who haven’t yet made the commitment to being fully automated,” says Kevin Keane, product strategy manager for software developer SigmaNEST. “It gives the customer a progressive roadmap on the way to connecting the shop to the ERP system.”
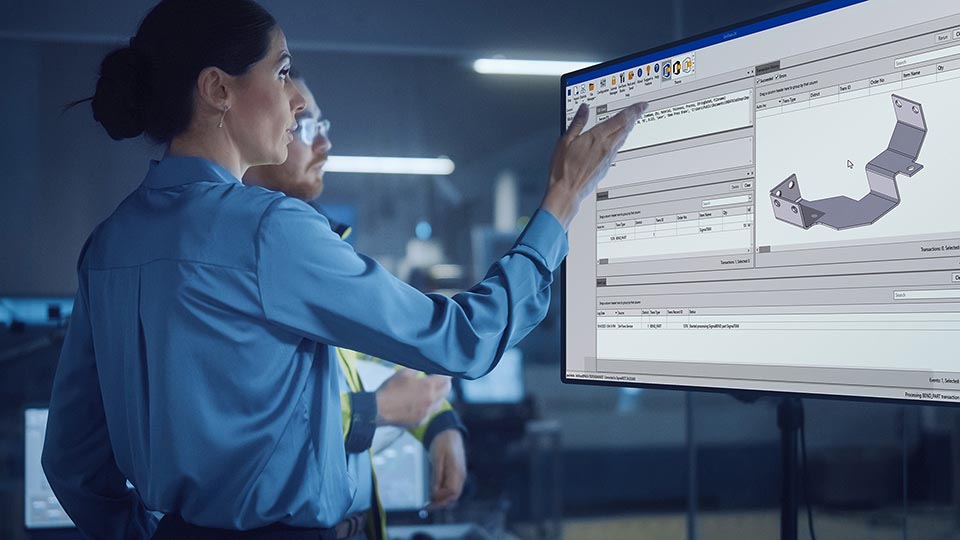
SimTrans was developed by Cincinnati-based SigmaNEST, a provider of business systems software that integrates fabrication process data to optimize shop floor production. The company also develops CAM software and manufacturing ERP software. Version 24 of SimTrans was launched Dec. 11, 2023.
It’s a more reliable system, eliminating human errors. And it saves the fabricator mountains of time.
Listening to The Data
“SimTrans automatically transfers data relating to materials, parts and job work orders,” says Keane. For example, when a fabricator enters a new order into the MRP/ERP system, SimTrans automatically communicates the information to targeted applications in real time. In this way, SimTrans provides a continuous data link enabling the ERP to be synchronized to the shop.
“In a sense, SimTrans’s job is to sit there in the middle and listen,” explains Keane. As soon as there is a new work order, SimTrans jumps into action. “It transfers the work over without anyone needing to type in the work order information. So it’s a more reliable system, eliminating human errors. And it saves the fabricator mountains of time,” Keane notes.
Empowering
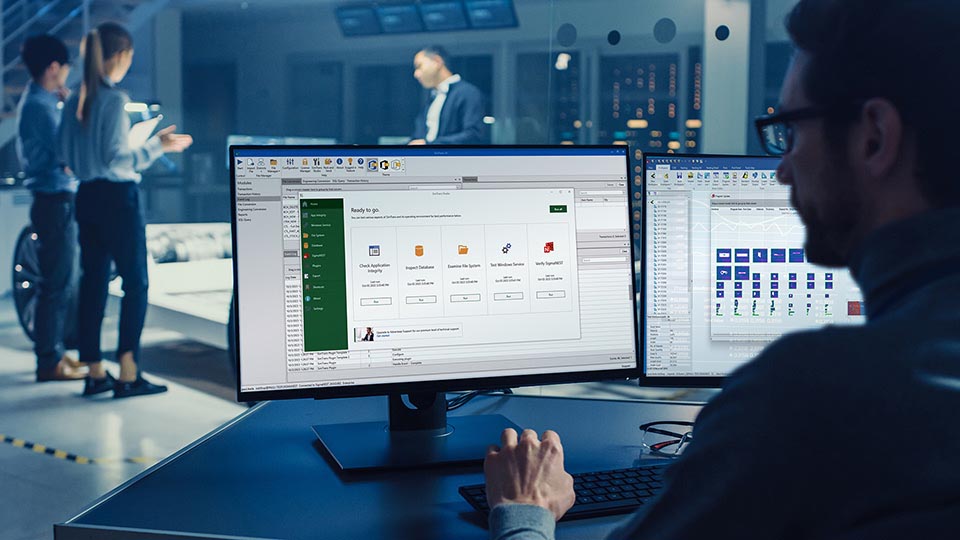
The 2024 version of SimTrans makes strides in empowering the end user to be self-sufficient. “It is a business-critical software,” notes Keane. The software is expected to perform 24/7/365. “The new SimTrans Studio diagnostic tool within SimTrans ensures everything is in working order and reports on the status of the system,” Keane says.
The advanced diagnostics capabilities built into Version 24 helps streamline customer service. There is a built-in battery of tests the software uses to determine if all of the environmental conditions are correct, and whether the key functions are working.
"The upgrade makes it much easier for the customer’s IT team and our own support staff to troubleshoot the system. We realize that SimTrans is a 24/7-critical software for manufacturers,” Keane reports. “Customers have the same need for uptime on their software as they do for the shop floor equipment.” Other features of SimTrans include being able to view project status from tablets or cell phones and receiving automated reports via email. Existing orders can also be seamlessly modified.
Universal Compatibility
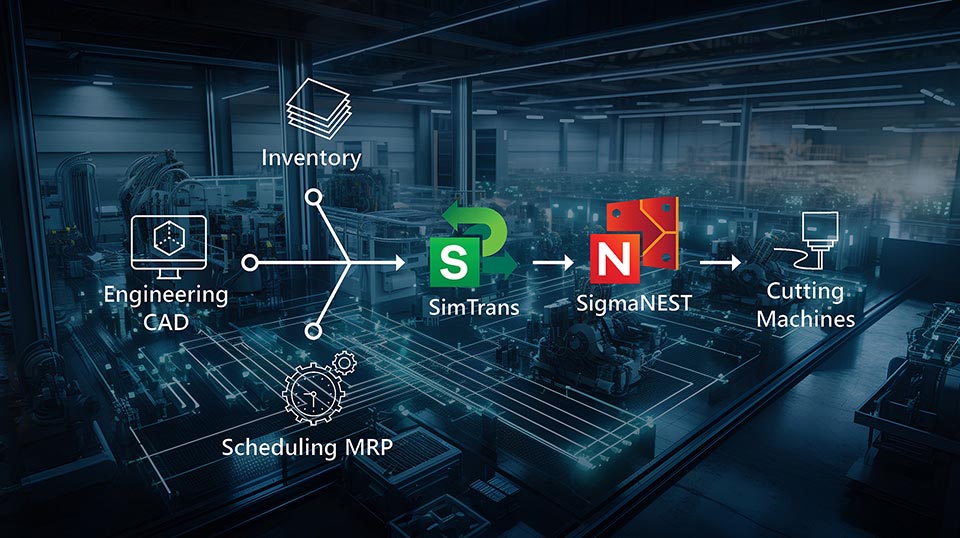
SimTrans is based on being universally com- patible. “Our customers have any number of different MRP systems and ERP systems. At SigmaNEST we have a standard, out- ward-facing interface designed to be easy for third parties or customers to connect and share data. SimTrans is plug-and-play, for easy compatibility,” assures Keane.
SimTrans is compatible with common file types and SQL databases. And the software comes loaded with 40 ready-to-use standard transaction types designed for typical fabricator needs, ranging from material stock management to work order transfer. “SimTrans is silently working to keep the systems in lock-step,” notes Keane. Changes on the front end are passed immediately to the shop.
SimTrans is also integrated with SigmaNEST, the developer’s cornerstone product. “By interfacing with SigmaNEST CAD/CAM software, invalid part geometry files are separated out and tagged for repair. It is easy to correct any geometry issues before releasing the order for production,” says Keane.
Reverse Reporting
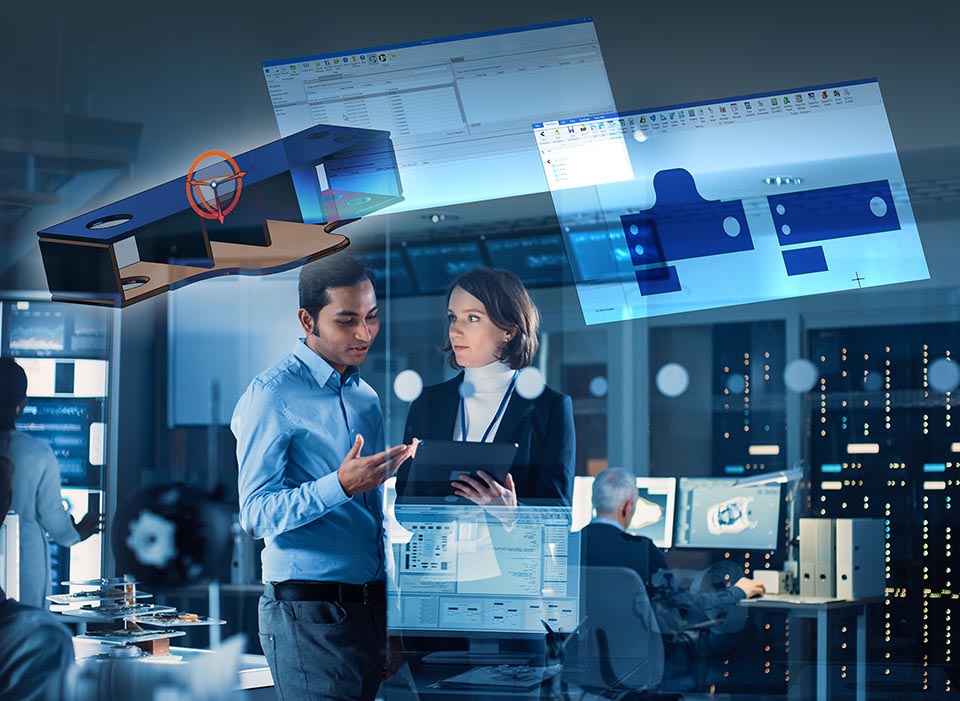
If the shop floor makes a change, it is also reported up through SimTrans,” explains Keane. “This automatic feedback means fabricators can complete projects faster and achieve lights out, full end-to-end automatic machine operation, using batch operations,” Keane notes.
The 2024 version of SimTrans features a feedback function that reports information back upstream to the parent ERP system. SimTrans can be configured to report upstream based on any number of triggers or events. After a machine has finished a particular job, or if a certain amount of material has been consumed, SimTrans can report that. This feature was reinvented for 2024 with transparency and self-sufficiency in mind.
“In prior versions of SimTrans, this was not as easy to achieve. This is a marked improvement. It is more important today than it ever was for customers to have their data accessible in a way that provides insight about how they work, and how they can improve,” Keane notes.
For customers with multiple sites, SimTrans is scalable. “It can easily be an enterprise tool for a customer with a thousand employees or a job shop with eight people,” reports Keane. “You can think of it as a transaction broker that sits between the systems and does the mundane but vital work of moving the information back and forth,” he says.
Published in FFJOURNAL STAFF, January 2024
"Listen, Then Act" by Kevin Keane, Product Strategy Manager, SigmaNEST