No mundo do arranjo, o trabalho com tubos pode ser bem diferente do trabalho com chapas. Com a chapa, há um nível de liberdade de arranjo que os fabricantes não têm com o tubo. O arranjo tende a ser mais aberto, e as fábricas podem arranjar ao longo do comprimento e da largura da chapa, enquanto no lado do tubo, como estão trabalhando com apenas uma direção e a peça ocupa a maior parte do espaço, há muito menos espaço para erros. As fábricas precisam ser muito melhores na otimização do arranjo de tubos, pois a menor diferença na ordem ou orientação da peça pode realmente prejudicar a utilização.
Equívocos comuns
De uma perspectiva mais geral de aproveitamento, não é incomum que os fabricantes que estão trabalhando com software de arranjo queiram tentar realizar o arranjo manual. Em alguns casos, esses fabricantes acham que podem fazer sozinhos o que o software foi projetado para fazer. Embora alguns tenham o discernimento necessário para criar um arranjo apertado, eles podem levar horas para chegar a resultados que o software de arranjo poderia determinar em minutos.
Quase sempre, o software oferece resultados tão bons ou melhores em uma fração do tempo. No entanto, pode ser difícil quebrar essa mentalidade manual. Com uma geração mais jovem entrando no espaço de fabricação, é menos comum ver essa dependência do arranjo manual, tanto no lado da placa quanto no lado do tubo. E, após testes lado a lado, o software de arranjo prova sua eficiência e versatilidade.
Quando se trata de processamento de tubos, muitas fábricas não percebem como a qualidade do material pode ser variada. Quando estão trabalhando com máquinas manuais, como serras, a variabilidade do material é menos problemática. Mas quando essas lojas deixam de trabalhar com máquinas manuais e passam a trabalhar com máquinas de corte CNC, essa variabilidade pode causar problemas.
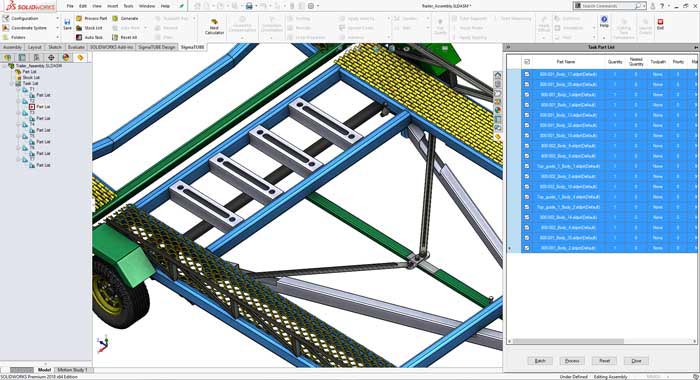
Uma máquina CNC pode detectar até mesmo as menores alterações no material. Se a máquina não tiver algo como o apalpador para ajustar essa pequena diferença de material, os fabricantes podem acabar recebendo peças com aparência um pouco diferente da esperada, especialmente em comparação com peças cortadas manualmente. É importante levar em conta a variabilidade do material sempre que possível.
O tubo retangular apresenta um desafio adicional relacionado à variabilidade do material. Não é incomum que o raio varie em um tubo retangular. Quando um programa baseado em um tamanho ou raio específico de estoque é gerado, a qualidade do corte pode ser prejudicada se o modelo CAD não for alterado para refletir com precisão o material real que está sendo cortado.
Arranjo para capacidades da máquina
Uma das primeiras coisas que uma fábrica precisa considerar quando se trata da otimização do processamento de tubos é o arranjo com base no tipo de máquina de corte com a qual está trabalhando.
O arranjo pode funcionar para tudo, desde uma simples máquina de serra que faz apenas cortes finais até máquinas a laser complexas com recursos avançados de manuseio e carregamento/descarregamento de peças. No entanto, os recursos de arranjo estão diretamente relacionados ao tipo de máquina que está sendo usada.
Nas máquinas de serrar, o software de arranjo precisará conhecer parâmetros específicos, como, por exemplo, se o corte será feito em feixes. O software otimizará o arranjo para garantir que a serra possa cortar o maior número possível ao mesmo tempo.
Com uma máquina a laser padrão, é importante entender que alguns dos sistemas de mandris podem deixar uma zona morta significativa no bastão. Por exemplo, se os mandris estiverem segurando um comprimento de 10 a 20 pol. na extremidade do bastão, a tocha não conseguirá acessar essa área e, portanto, não poderá cortá-la.
Nesses casos, algo como um recurso de arranjo de zona morta pode ajudar a maximizar o uso do material. Com esse recurso, os fabricantes fornecem ao software todas as peças e o software as analisa para ver se alguma é simples ou longa o suficiente para ser colocada nessa zona morta, de modo que a extremidade da vara possa ser usada. Desde que não haja recursos de corte, a peça provavelmente será colocada nessa zona morta.
Em máquinas mais avançadas com sistemas complexos de carregamento de peças e manuseio de materiais, os sistemas de mandris também entram em ação. Por exemplo, algumas máquinas de corte de tubos têm quatro mandris grandes que são capazes de realizar todo o manuseio de material e estoque. Esse tipo de máquina e sistema de mandris é capaz de alternar do corte à esquerda-direita para o corte à direita-esquerda trocando os mandris. O algoritmo de arranjo no software precisa saber sobre esses processos para aproveitar esse recurso da máquina. Os fabricantes podem simplesmente informar ao mecanismo de arranjo em que máquina estão trabalhando e ele examinará todos os recursos e capacidades disponíveis para aproveitá-los ao máximo e fazer o aproveitamento de acordo.
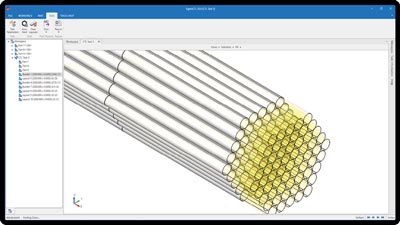
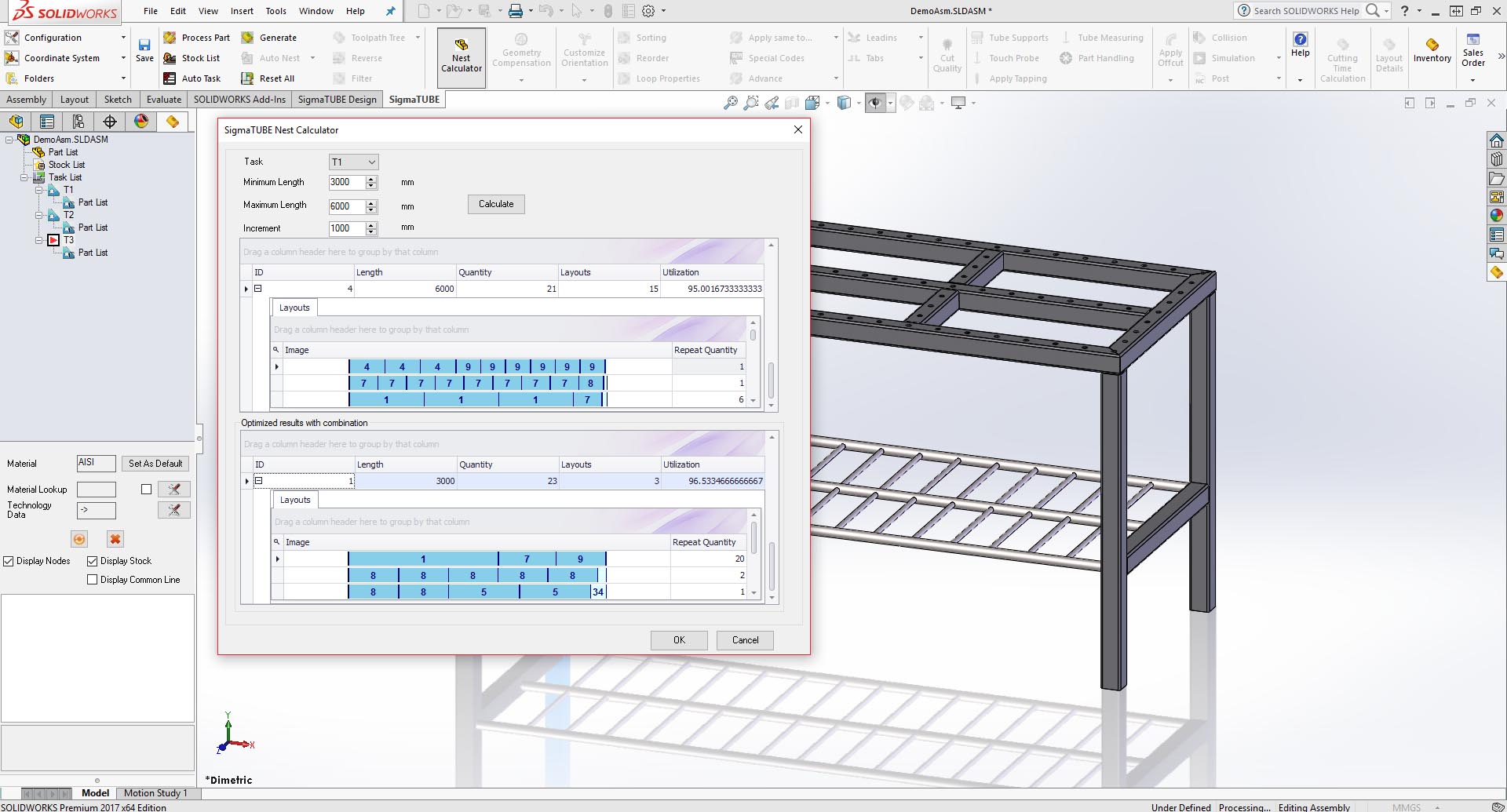
Arranjo para otimização de materiais
O suporte para corte em linha comum é uma ótima maneira de otimizar o uso do material. No entanto, é importante observar que, quando o arranjo 1D para máquinas de tubos é realizado, o uso de um corte de linha comum em vez de uma distância de corte pode ser a diferença entre encaixar mais uma peça na extremidade do bastão.
Para máquinas de corte não chanfradas, recursos como a compensação de 4 eixos podem ser de grande ajuda para ajustes adequados no processo de montagem. O corte de material extra em geometrias de chanfro ou cope usando esse recurso garantirá um ajuste bom e limpo no interior do tubo com qualquer componente ao qual ele esteja sendo soldado nos estágios subsequentes.
Nesses casos, o mecanismo de arranjo pode examinar o caminho da ferramenta em vez da geometria real da peça 3D para determinar a proximidade entre as peças que podem ser arranjadas. Como o caminho da ferramenta determina a aparência da peça acabada, o software pode fazer o arranjo um pouco mais apertado com esse recurso.
O arranjo pode funcionar para tudo, desde uma simples máquina de serra que faz apenas cortes finais até máquinas a laser complexas com recursos avançados de manuseio e carregamento/descarregamento de peças.
Arranjo para execução de programa otimizado
Para o processamento de tubos com máquinas a laser, normalmente os fabricantes trabalham com feixes do mesmo comprimento de bastão. A maioria está comprando de um fornecedor que fornece em dimensões muito específicas; 240 pol. é uma dimensão comum.
Se um fabricante estiver trabalhando com o mesmo comprimento de haste, o software de arranjo pode ser instruído a otimizar a criação de arranjos exatos em vez de otimizar o material. O mecanismo dará uma olhada nas peças e descobrirá a melhor utilização para um bastão e repetirá esse programa várias vezes.
Para os fabricantes que trabalham com diferentes comprimentos de varas, é importante garantir que o software permita a otimização da melhor combinação. Se o mecanismo tiver dois comprimentos diferentes inseridos, ele poderá determinar a melhor combinação de varas para otimizar a utilização do material do estoque da fábrica.
O arranjo também pode permitir que os fabricantes especifiquem o comprimento que desejam usar. Por exemplo, uma loja pode especificar que o software use todos os comprimentos mais curtos primeiro para passar pelo maior número possível de remanescentes antes de passar para o estoque real.
A criação de arranjos que otimizam as execuções de programas em vez de material faz sentido para as fábricas que produzem lotes muito grandes, onde há milhares de peças a serem cortadas. Pode ser mais vantajoso financeiramente para elas reduzir o tempo que um operador gasta para retirar e classificar peças diferentes, pois os programas de arranjo diferem muito de uma peça para outra.
Como não estão fazendo muito descarregamento ou outras operações, as fábricas de baixo volume/alta mistura podem aumentar todas as configurações de otimização para garantir que a utilização do material seja maximizada. Realmente faz mais sentido priorizar o material do que a otimização do programa nessas aplicações.
É importante que os fabricantes analisem os controles e vejam o que funciona melhor para as necessidades da fábrica. Por exemplo, se uma fábrica estiver trabalhando com grandes lotes, a máquina poderá incluir recursos mais avançados, como carregamento e descarregamento. Nesse caso, não importa se todos os programas são diferentes, pois a máquina é capaz de processar rapidamente e tomar o lugar do operador, liberando-o para outras tarefas. Um bom software de arranjo oferece às lojas a capacidade de ajustar os mostradores e as otimizações conforme acharem necessário.
O arranjo pode funcionar para tudo, desde uma simples máquina de serra que faz apenas cortes finais até máquinas a laser complexas com recursos avançados de manuseio e carregamento/descarregamento de peças.

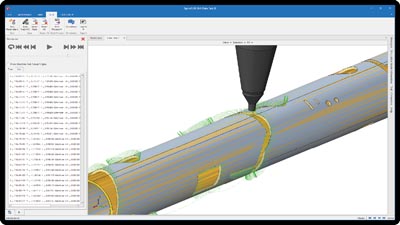
Cálculo de tempo e custo
Uma calculadora é outra boa ferramenta para se ter quando se trata de processamento de tubos. Uma das principais vantagens é que a calculadora permite que as fábricas insiram métricas e determinem o tempo e os custos sem precisar gerar o programa para a máquina.
Os fabricantes podem simplesmente digitar todos os diferentes comprimentos de varas disponíveis no chão de fábrica e podem até mesmo especificar com qual comprimento começar e trabalhar. A calculadora do software de arranjo analisa todos os aspectos e determina o melhor processo resultante com base nos comprimentos de varas disponíveis ou até mesmo nos melhores comprimentos de varas para um determinado lote.
Esse é um ótimo recurso para licitar trabalhos. Ele oferece às lojas a flexibilidade de verificar se um trabalho vale a pena e combinar os comprimentos de vara disponíveis para otimizar o uso do material.
Publicado na Canadian Fabrication & Welding, fevereiro de 2022
"Tackling Tube Nesting", por Lindsay Luminoso, Editora Associada
https://www.canadianmetalworking-digital.com/february-2022/Tackling-Tube-Nesting
Entrevista com Dakota Baird, proprietário de produto para tubo/barra e importação do SigmaNEST